Insert Molding and Insert Molding Machines: Process, Features, and Advantages
At Kinki Machinery, we understand that manufacturing is more than just a process; it’s the foundation of progress and innovation. As industries demand faster production cycles, tighter tolerances, and stronger multi-material parts, insert molding has become a go-to solution.
Insert molding machines—especially vertical injection models—are specifically designed to streamline insert placement, ensuring high precision and low-defect results. Our advanced insert injection molding machines—including our flagship vertical injection molding systems—are built around the principles of insert molding, enabling manufacturers to combine metal and plastic into robust, hybrid components in a single, streamlined process. Whether you’re producing medical devices, TPU-based components, or electronic parts, our machines offer unmatched flexibility and control. This article explores how insert molding works, what features to look for in a high-performance machine, and why more manufacturers are adopting this technology.
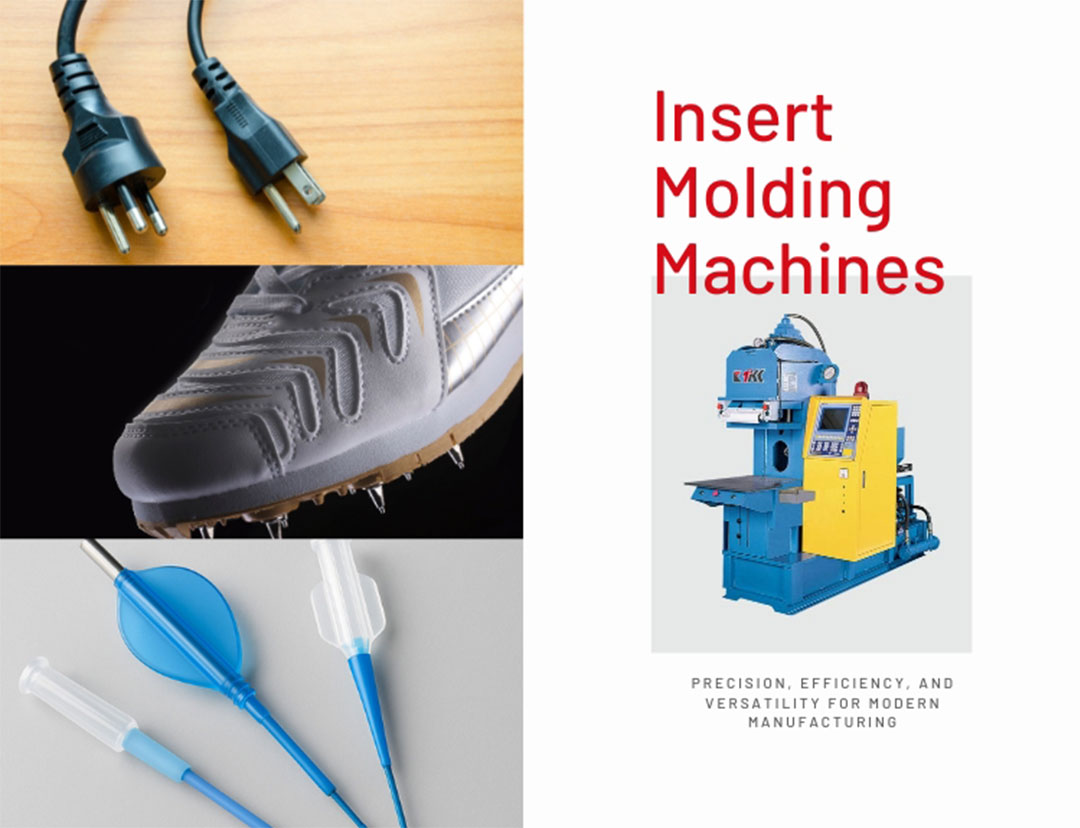
What is an Insert Molding Machine?
To understand the role of an insert molding machine, it’s important to first understand the insert molding process itself.
Insert molding machines are precision-engineered systems that integrate pre-formed components—such as pins, bushings, screws, or terminals—into plastic parts during the molding cycle. By combining these materials, our machines produce components that are not only durable but also highly functional.
While metal is the most commonly used insert material, insert molding can also incorporate plastic, ceramic, or composite inserts depending on the design requirements.
Unlike conventional manufacturing methods that require separate assembly stages, insert molding eliminates inefficiencies, reducing production time, labor costs, and material waste. The result? High-quality, ready-to-use products that drive innovation.
Insert Molding vs. Overmolding: What's the Difference?
As insert molding gains popularity across industries, it’s often compared with another process: overmolding.
-
Insert molding
embeds a pre-existing component directly into the mold, creating a single, solid piece. -
Overmolding
adds an extra layer of material—like soft-touch rubber over a rigid plastic core—to enhance grip and comfort.
Compared to horizontal systems, vertical insert molding machines simplify insert placement and reduce misalignment—making them a preferred choice for insert molding. Choose insert molding when your application requires the combination of metal and plastic for superior strength and conductivity, and opt for overmolding when multi-material products with varied textures are needed. For a deeper dive into these technologies, check out our comprehensive guide on Everything About Rubber Injection Molding and Overmolding Solutions.
The Insert Molding Process
In insert molding, a pre-manufactured component (such as a metal insert or electronic part) is placed into a mold cavity, and molten thermoplastic resin is injected around it to form a seamless, unified component. The plastic solidifies, forming a strong mechanical bond with the insert and resulting in a fully integrated part.
The mold cavity must be precisely designed to both accommodate the insert and ensure optimal resin flow for complete encapsulation and bonding. This process is ideal for creating strong, integrated parts without additional assembly steps.
Industries that demand high part strength, conductivity, and performance—such as automotive, electronics, and medical devices—benefit tremendously from this method.
Medical and TPU Insert Molding Applications
Insert molding is widely used in the medical field, especially for components like catheter hubs or hypotube connectors where plastic–metal integration is critical. Our machines are also compatible with flexible materials such as TPU, which can be used in wearable medical devices requiring both durability and softness—all achievable within the insert molding process.
Insert Molding Advantages: Why Manufacturers Prefer This Process
Insert molding offers several key benefits over traditional multi-step manufacturing or post-assembly bonding:
-
Material Integration
: Combines plastic with pre-formed components (e.g., metal, ceramic, or plastic inserts) to eliminate post-molding assembly. -
Structural Strength
: The injected plastic forms a strong mechanical bond with the insert, improving durability. -
Cost-Efficiency
: Reduces production steps and manual labor, lowering overall manufacturing costs. -
Design Flexibility
: Supports complex geometries and embedded components that are difficult to achieve through conventional molding methods. -
Improved Functionality
: Inserts can provide molded-in threads, mounting points, or electrical terminals, eliminating the need for post-mold machining or secondary assembly.
These advantages make insert molding a preferred solution across high-precision, high-efficiency manufacturing environments.
Advanced Features of Kinki Insert Molding Machines
Our Insert Molding Machines are engineered with cutting-edge features that deliver unmatched precision, efficiency, and flexibility. Here are the key capabilities that set our machines apart :
-
High-Speed Production and Short Cycle Times
Kinki’s machines can achieve cycle times as low as 10-20 seconds, depending on the complexity of the insert and material used. This rapid production is ideal for industries that need to respond quickly to market demands. For example, our vertical injection molding machine is designed for high precision and fast cycle times, while our horizontal models support high-volume production with consistent quality.
-
Precision Injection and Material Control
Equipped with high-precision injection units, our machines ensure consistent material flow and tight tolerances throughout production. Closed-loop control systems continuously monitor and adjust injection pressure, temperature, and speed in real time—minimizing defects and ensuring uniform quality. This level of control is critical in applications like medical devices and electronics, where even slight variations can be significant.
-
Versatility in Material Compatibility
Our machines process a wide range of materials, including engineering plastics (such as ABS and polycarbonate), elastomers, and various metals (like stainless steel and aluminum). This versatility allows manufacturers to produce hybrid components that combine the best properties of different materials. Whether you’re exploring robust insert molding or innovative TPU injection molding techniques, our technology adapts to meet demanding applications.
-
Customizable Mold Designs for Complex Geometries
We support custom mold configurations that enable the production of intricate, multi-part components. Advanced mold simulation software optimizes each design for maximum production efficiency, reducing errors and material waste. This flexibility is especially valuable for manufacturers seeking to incorporate unique design elements or seamlessly integrate inserts.
-
Energy-Efficient Technology
Our machines incorporate energy-saving features, such as variable frequency drives (VFDs), which optimize motor speeds based on production demands. This not only reduces power consumption but also lowers operational costs—contributing to a more sustainable manufacturing process. Energy efficiency remains a priority in our TPU injection molding systems as well.
-
Precision Clamping Systems
Our precision clamping systems ensure consistent pressure across the mold, a key factor in producing parts with intricate designs or delicate inserts. The adjustable clamping force allows operators to fine-tune the process according to part geometry, ensuring minimal defects and superior product quality.
-
Automation and Accurate Insert Placement
State-of-the-art robotic automation minimizes human error by ensuring accurate insert placement every time. This not only accelerates production but also guarantees a robust bond between plastic and metal components. For troubleshooting any issues that might arise, our vertical injection molding machine troubleshooting guide provides practical tips and solutions to maintain peak performance.
How to Choose the Right Insert Molding Machine?
When selecting an insert molding machine, ask the following:
- What materials are you working with—TPU, ABS, PC, or medical-grade polymers?
- What is the size and complexity of the insert part?
- Does your application require high-speed or precision placement?
- Is vertical clamping preferable for better insert accessibility?
At Kinki, we offer a full lineup of vertical insert molding machines tailored to diverse production needs. From the KR Series for large, high-pressure applications, to the KC Series with a compact, tie-bar-less design for mid-size parts, and the KT Series ideal for small to medium components in space-constrained environments—we have the right solution for every scale.
For manufacturers seeking energy efficiency and precision, our KET Series offers all-electric vertical molding. We also provide Special Purpose Machines with fully customized specifications to meet unique insert molding challenges across medical, automotive, and electronics sectors.
Technical Specifications
Kinki Machinery offers a diverse lineup of vertical injection molding machines designed specifically for insert molding applications—from small precision parts to large hybrid components. Below are key models and their technical highlights :
-
KR Series – Large-Scale Insert Molding
Vertical Clamping / Horizontal Injection
Ideal for large-sized insert molding applications. Features a long stroke and large injection volume to handle large parts and high injection pressure requirements. -
KC Series – Tie-Bar-Less Mid-Size Machine
Vertical Clamping / Horizontal Injection
Compact and efficient design with a three-sided open space for easy mold access. Optimized for medium-sized insert molding. -
KT Series – Compact Machine for Small to Medium Parts
Vertical Clamping / Vertical Injection
Equipped with a double-cylinder injection system and straight-pressure clamping. Easy to install and operate in limited spaces. -
KET Series – All-Electric Vertical Machine
All-Electric Vertical Design
Delivers superior performance with energy-saving, precise control, and minimal environmental impact—ideal for sustainable manufacturing. -
Special Purpose Machines – Fully Customized Solutions
Tailored to Your Application
Built-to-order machines with customizable sizes and features, optimized for unique product requirements and production goals.
For detailed specifications, CAD drawings, or configuration support, please contact our technical team.
Case Study : Transforming Insert Molding Efficiency Across Key Industries
Background :
Leading manufacturers in the 3C electronics, sportswear, and medical device industries increasingly face the challenge of producing compact, durable, and high-precision components. Traditional molding and assembly methods led to longer cycle times, inconsistent quality, and high production costs—especially for products like power plugs, cleated shoe soles, and hypotubes.
Challenge :
To maintain competitiveness, these manufacturers required a more integrated molding solution—one that could reduce reliance on manual assembly, improve part consistency, and scale efficiently across different product lines.
Solution :
By implementing Kinki’s Insert Molding Machines—particularly the KC and KET series—manufacturers achieved :
- High-Speed Cycle Times : Reduced to 10–20 seconds for plug connectors and cleat parts.
- Improved Precision : Closed-loop injection control minimized variation in medical hypotube overmolding.
- Automation Integration : Robotic insert placement reduced human error and ensured consistent quality.
- Custom Mold Flexibility : Enabled rapid changeovers across diverse mold sizes and geometries.
- Energy Efficiency : All-electric KET series reduced power consumption during high-volume runs.
Results :
Clients across these industries reported up to 30% faster production cycles, 20–25% improvement in part quality, and greater agility to respond to changing market demands—proving that Kinki Machinery’s insert molding technology delivers across highly specialized sectors.
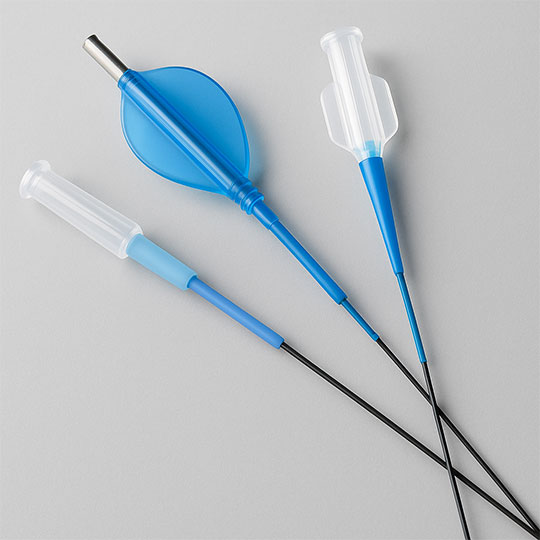
Applications Across Industries
Our Insert Molding Machines serve diverse sectors :
-
Automotive :
From switches to gears and dashboard elements. -
Electronics :
Precision connectors, plugs, and housings. -
Medical Devices :
Biocompatible parts for diagnostic and surgical instruments. -
Home Appliances :
Durable knobs, handles, and other functional components.
These examples complement our extensive work in other fields, such as TPU injection molding for consumer goods and power cord molding for electrical applications, reinforcing our versatile expertise.
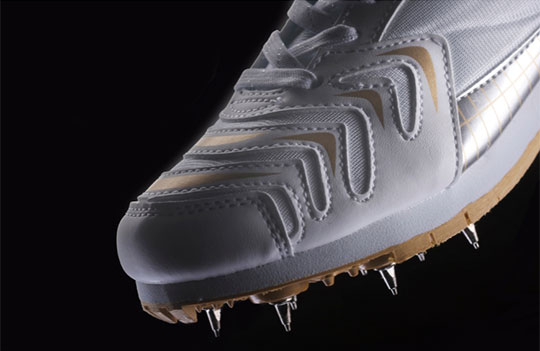
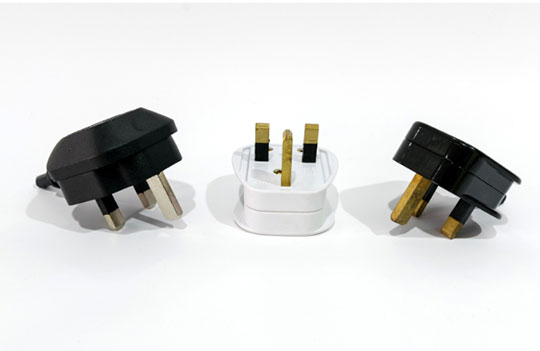
Why Choose Kinki Machinery?
When you choose Kinki Machinery, you're not just purchasing a machine—you’re forming a lasting partnership. Our innovative solutions and customer-first approach ensure that your production line operates at peak efficiency. With decades of experience and a proven track record, we have established ourselves as a trusted name in manufacturing technology. We don’t just meet expectations; we exceed them.
Technical Support and Customization
Understanding that every manufacturing process is unique, we offer comprehensive technical support and customization services. Whether it’s optimizing mold design or integrating automated features, we work with you to ensure your setup achieves maximum efficiency. If you encounter any issues, our detailed vertical injection molding machine troubleshooting guide is available to help quickly resolve any challenges.
Ready to Build Stronger, Smarter Components?
Whether you're producing medical TPU parts, automotive inserts, or electronic connectors, our insert injection molding solutions deliver strength, precision, and speed.
Contact our technical team to explore the right machine for your application or request a tailored quote.